Pressure vessels, designed to contain gases or liquids at pressures significantly different from the surrounding atmosphere, are fundamental in various industries. These containers are vital in sectors like petrochemicals, oil and gas, and aerospace, where safety, durability, and performance are paramount.
Pressure vessel fabrication combines engineering precision, strict adherence to standards like those from the American Society of Mechanical Engineers (ASME), and the use of specific materials. This process confirms each vessel safely handles the intended pressures and stresses.
This introduction will further discuss the importance of standards in fabrication, material selection, design optimization, and the advanced processes involved in creating these essential components.
The aim is to highlight the complexity and critical nature of pressure vessel fabrication, underscoring the need for expertise and innovation in this field.
The Role of Standards in Pressure Vessel Fabrication
Adhering to established standards in the fabrication of pressure vessels is foremost for ensuring their safety and reliability.
The ASME Boiler and Pressure Vessel Code ASME Code (BPVC), specifically Section VIII, plays a pivotal role among these guiding principles. It outlines rigorous guidelines covering the design, fabrication, inspection, and testing processes that pressure vessels must undergo before they are deemed safe.
ASME’s Boiler and Pressure Vessel Code
The ASME first issued the BPVC in 1911 as a set of universally recognized safety standards to regulate the design, manufacture, installation, inspection, and care of boilers, nuclear components, and other pressure vessels. Section IX of this code relates specifically to the qualification of welders, welding operators, brazers, and brazing operators and the procedures they employ in welding and brazing these items.
Material Selection for Durability and Performance
Selecting materials in pressure vessel fabrication is a critical factor that directly influences their durability, performance, and suitability for specific applications. Two of the most commonly used materials are stainless steel and carbon steel, each offering distinct advantages that cater to varying operational demands and environmental conditions.
Stainless steel is renowned for its exceptional corrosion resistance, making it an ideal choice for pressure vessels that operate in corrosive environments or handle corrosive substances. Its ability to withstand the detrimental effects of rust and other corrosive elements extends its life span, ensuring long-term reliability and safety. Stainless steel’s inherent strength and resistance to high temperatures further enhance the performance and durability of pressure vessels in demanding conditions.
Carbon steel is favored for its robustness and cost-effectiveness, especially in applications where corrosion is not a primary concern. Its high tensile strength means pressure vessels can withstand substantial pressure, making it suitable for various industrial applications. Additionally, carbon steel can be treated with coatings or additives to improve its corrosion resistance, versatility, and applicability in diverse operations.
Manufacturers can choose the most appropriate material by carefully considering factors such as the operational environment, the substances to be contained, and the specific performance requirements.
Click here for a complete list of materials Baker Industries can use for your current or upcoming pressure vessel fabrication project.
Designing Pressure Vessels for Optimal Performance
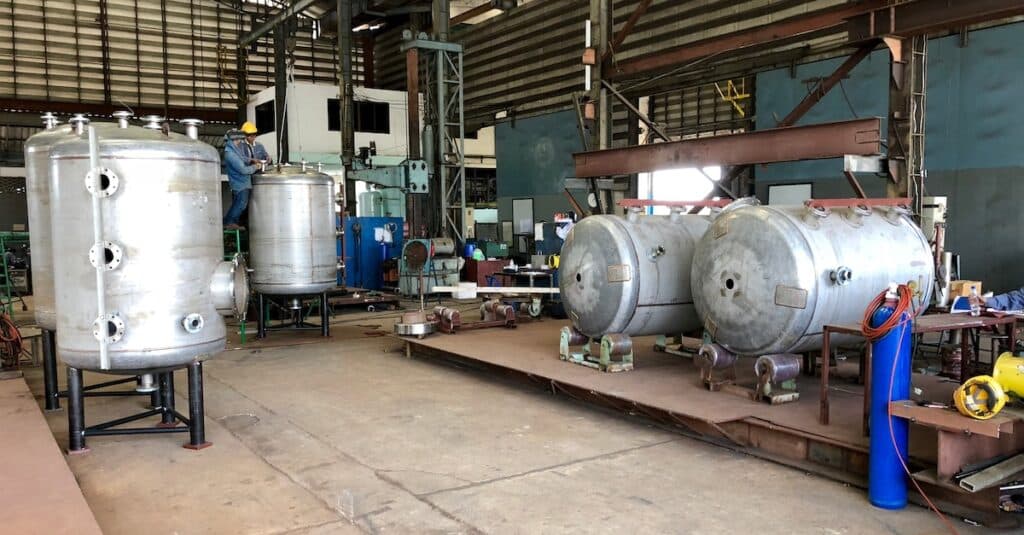
Design considerations in pressure vessel fabrication are central to vessels operating safely under high pressure and meeting specific industry needs. Carefully balance the structural integrity, material properties, and compliance with rigorous standards, notably the ASME Boiler and Pressure Vessel Code. This code provides the foundational framework for designing vessels to withstand the operational stresses they are likely to encounter and to make sure they perform reliably throughout their service life.
In designing high-performance pressure vessels, engineers must examine several key factors.
First, the vessel must endure the specific pressure and temperature conditions of its intended application, necessitating a precise thickness and material strength calculation.
As previously discussed, material selection impacts the vessel’s ability to resist corrosion and maintain its integrity under extreme temperatures and pressures.
Additionally, the vessel design must be based on its intended use, including the type of substances it will contain and the environment in which it will operate. Engineers must select the appropriate materials and design features to prevent contamination, facilitate maintenance, and ensure easy access.
Advanced simulation tools and stress analysis techniques are often employed to model the vessel’s behavior under various conditions, further optimizing the design for safety, efficiency, and longevity.
The Fabrication Process: From Planning to Production
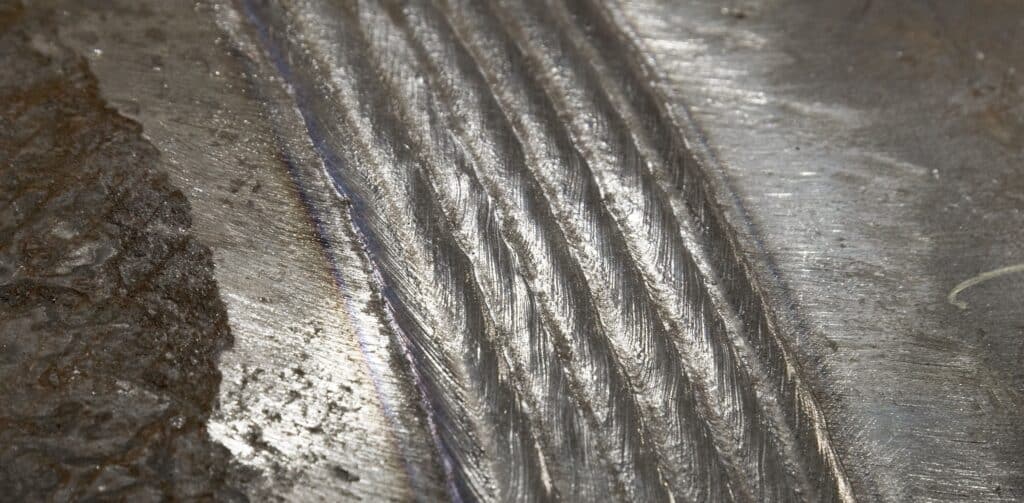
The fabrication process of pressure vessels is often a complex and multi-stage operation that requires precision, expertise, and adherence to strict standards. This process is broadly outlined in the following steps, emphasizing the importance of advanced fabrication techniques.
1. Design and engineering: The first step involves detailed planning and design, adhering to the ASME BPVC, among other standards. This phase includes material selection based on the vessel’s intended use, pressure, temperature conditions, and corrosion resistance requirements. Advanced computer-aided design (CAD) and finite element analysis (FEA) tools are used for accurate modeling and stress analysis.
2. Material procurement: Once the design specifications are set, selecting the right materials is the next critical step. High-quality stainless steel and carbon steel are staples for their durability and resistance. Titanium, known for its exceptional strength-to-weight ratio, and nickel alloys such as Inconel and Hastelloy, are frequently chosen for their superior corrosion resistance and ability to maintain structural integrity under extreme temperatures. These materials are especially common in pressure vessels serving as flight hardware, including fuel tanks for aircraft and spacecraft, where performance and safety cannot be compromised.
3. Cutting and forming: The next step is cutting and forming the materials into the designed shapes. Techniques such as plasma, waterjet, and laser cutting are employed for precision. The materials are then formed into the vessel’s shape using metal forming techniques such as rolling for shells and dishing for heads.
4. Welding: Welding is a fundamental phase in the fabrication process, requiring high skill and adherence to standards to ensure the vessel’s structural integrity. TIG (GTAW), MIG (GMAW), laser welding, and submerged-arc (subarc) welding are techniques often employed based on the specific requirements of each project. Laser welding offers precision and speed, ideal for complex or thin materials, while submerged-arc welding is favored for its deep penetration in thicker sections. All welding procedures are rigorously controlled and monitored to eliminate defects and ensure each vessel meets the highest standards of quality and safety.
5. Inspection and testing: Each vessel undergoes a rigorous inspection and non-destructive testing (NDT) to ensure conformance with quality standards and design specifications. Methods such as ultrasonic, radiography, and hydrostatic testing/inspection can detect imperfections and verify the vessel’s ability to withstand operational pressures.
6. Finishing: After passing all inspections, the vessel may receive final treatments such as stress relieving, sandblasting, and painting to protect against corrosion.
7. Quality assurance and documentation: The final step involves a comprehensive review of the vessel against client specifications and regulatory standards. Documentation of the fabrication process, testing results, and certifications confirm traceability and compliance.
These techniques enable fabricators to meet the demands of industries requiring custom pressure vessels, confirming their operations’ safety, reliability, and performance.
Ensuring Quality: Testing and Inspection
Ensuring the safety and quality of pressure vessels through testing and inspection is an indispensable part of the fabrication process.
The combined application of these testing and inspection methods means each pressure vessel meets the highest quality and safety standards before it enters service.
1. Quality control: Quality control includes verifying materials, monitoring fabrication techniques, and making sure welding procedures are performed correctly. It’s a proactive approach to prevent defects and ensure the vessel performs as designed.
2. Non-destructive testing (NDT): This testing method detects potential defects without damaging the vessel. NDT can identify issues that could compromise the vessel’s integrity or safety.
- Ultrasonic testing (UT): UT uses high-frequency sound waves to detect internal and surface discontinuities in materials. UT effectively identifies flaws such as cracks, voids, or inclusions within the welded joints and the vessel’s body. It provides a detailed assessment of the vessel’s structural integrity.
- Radiography testing (RT): RT involves using X-rays or gamma rays to produce images of the vessel’s internal structure on a radiograph film. RT is beneficial for detecting hidden flaws, such as porosity or cracks within welds. It is a visual record of the detected flaw and is invaluable in ensuring weld quality.
3. Inspection: Certified inspectors check each pressure vessel at various stages of the fabrication process. Inspections include visual examinations, dimensional checks, and reviewing welding procedures and qualifications. The final inspection confirms the pressure vessel meets all design specifications, standards, and regulatory requirements.
4. Hydrostatic testing: Hydrostatic testing subjects the vessel to pressures higher than its intended design to prevent leakage or structural weaknesses. This test simulates the vessel’s operating conditions and verifies its capability to safely handle its maximum allowed pressure.
5. Material traceability and documentation: As a final step, material traceability is a critical component in the quality assurance of pressure vessel fabrication, enabling the precise tracking of all materials to their origins. This ensures that every raw material or part used, such as pipes and flanges, can be traced back to its manufacturer, along with its material test certificates. This step is vital for identifying and addressing defective materials, ensuring compliance with quality standards, and facilitating efficient maintenance and repair.
Innovations in Pressure Vessel Fabrication
The landscape of pressure vessel fabrication is continually evolving, with recent innovations in fabrication techniques and materials pushing the boundaries of what’s possible in creating these essential components.
Advanced manufacturing processes and developing new materials are driving efficiency, safety, and functionality to unprecedented levels.
Advanced Manufacturing Processes
Adopting technologies such as additive manufacturing has revolutionized the fabrication of pressure vessels. This process can create components with complex geometries previously difficult or impossible to achieve with traditional manufacturing methods, giving engineers more freedom to customize pressure vessels to meet specific operational requirements and applications. It can also help cut down on material waste and cost.
Equally transformative is the integration of advanced automation and robotics into fabrication processes. Products from industry leaders like Lincoln Electric® exemplify this shift towards higher efficiency and precision. For instance, Lincoln Electric Automation’s ANNEX™ Robotic Positioners and Laser-Pak™ Robotic Laser Systems introduce unparalleled accuracy and versatility in handling and fabricating complex vessel designs.
Similarly, their Collaborative Welding Robots and Mechanized Welding Equipment streamline the welding process, ensuring consistent quality and reducing the potential for human error. Automated Cutting Equipment and Robotic Grinding Systems further demonstrate how automation can enhance the precision of component preparation and finishing, significantly boosting production rates.
These innovations in automation, exemplified by Lincoln Electric’s solutions, not only improve precision and reduce errors but also pave the way for increased production rates, underscoring a leap forward in the capabilities of pressure vessel manufacturers.
Materials Innovation
Developing new materials and enhancing existing ones leads to better performance under the demanding conditions in which pressure vessels often operate. Recent advancements have introduced high-strength, corrosion-resistant alloys, improving performance in extreme environments.
Materials such as Inconel, Hastelloy, and other nickel-based alloys are becoming more prevalent due to their ability to maintain integrity in high-temperature and corrosive settings.
Additionally, research into non-metallic composite materials is gaining traction for lighter, stronger pressure vessels with excellent corrosion resistance.
Application in Heat Exchangers and Reactors
These innovations are particularly impactful in designing and manufacturing heat exchangers and reactors, where efficiency, reliability, and safety are paramount. Advanced manufacturing techniques allow for the fabrication of heat exchangers with enhanced heat-transfer surfaces and reactors designed for optimal mixing and chemical resistance.
As a result, industries that rely on these components, from chemical processing to power generation, can achieve higher operational efficiencies and reduced downtime.
In summary, the ongoing advancements in fabrication techniques and materials are setting new standards in the pressure vessel industry.
These innovations enhance the performance and safety of pressure vessels and introduce new possibilities for their application across various sectors. Manufacturers aiming to lead in quality, efficiency, and innovation must stay abreast of the latest developments as their industry continuously evolves.
The Baker Industries Advantage in Pressure Vessel Fabrication
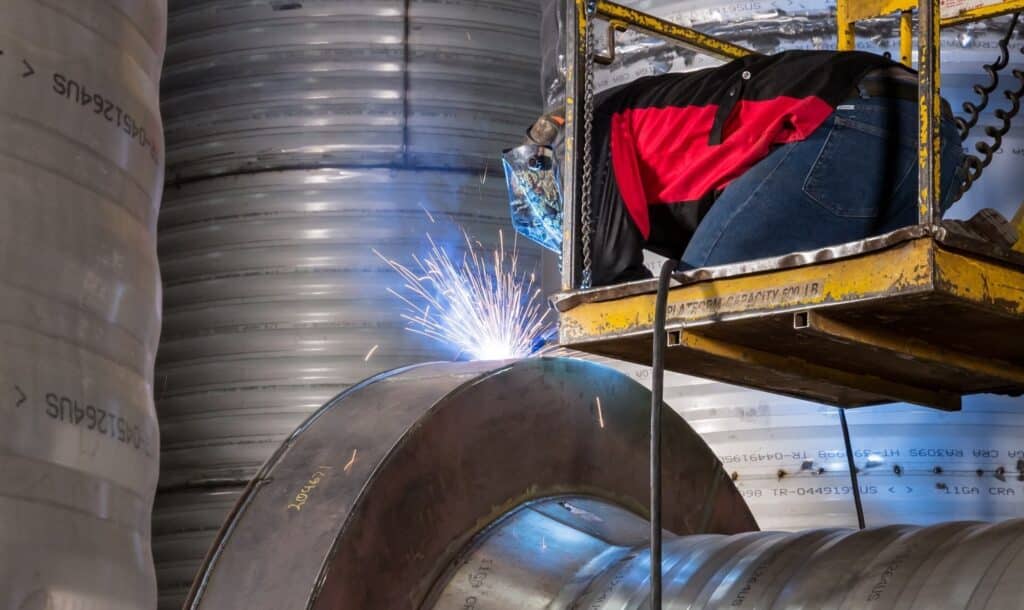
We ensure every product meets and exceeds the rigorous requirements of the ASME BPVC and other standards. Our commitment to quality guarantees the safety, reliability, and performance of your pressure vessel production projects.
To learn more about how Baker Industries can support your pressure vessel fabrication project needs or to discuss your project requirements in more detail, reach out to us at one of the links below.
Talk to an expert: https://www.bakerindustriesinc.com/contact-us/
Request a quote: https://www.bakerindustriesinc.com/contact-us/request-a-quote/