Metal additive manufacturing (AM), also known as metal 3D printing, is a critical technology reshaping how the manufacturing industry thinks about production speed and quality.
At Baker Industries, we recognize the transformative power of metal AM in offering unprecedented design freedom, efficiency, and customization capabilities. This article delves into metal AM, its historical evolution, and the core technologies driving its adoption across diverse industries.
Visit https://www.bakerindustriesinc.com/capabilities/3d-printing-services for more information on how Baker Industries’ metal additive manufacturing capabilities can assist with your current or upcoming projects.
Historical Context and Advancements in Metal AM Technologies
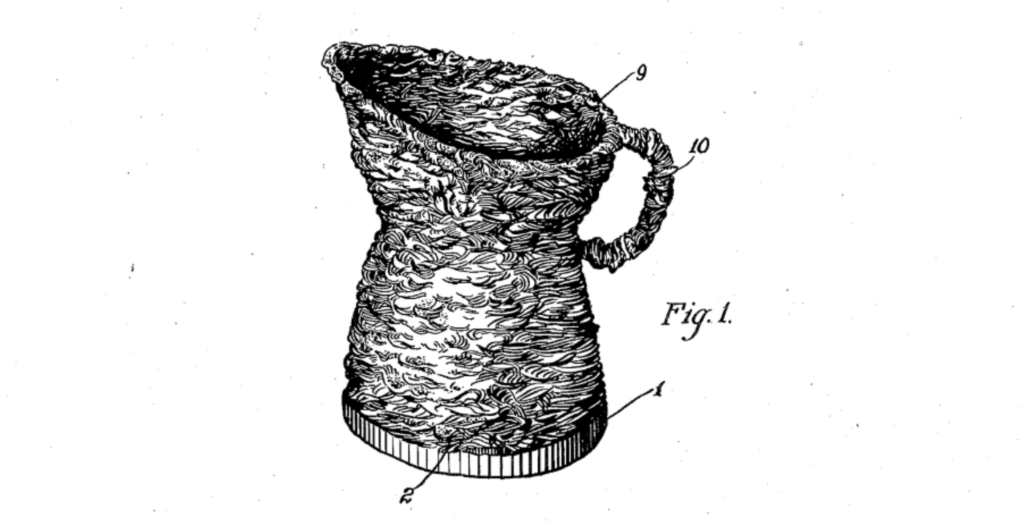
Metal am was initially conceptualized to produce decorative articles in the early 1920’s. Henceforth, the scope of metal AM has expanded thanks to advancements in machine precision, material science, and software algorithms.
Presently, metal AM technology has transitioned from prototyping to a central manufacturing process for end-use metal parts and tooling. Its significance today lies in its ability to produce complex components with reduced waste and shorter lead times.
This evolution is marked by the development of key technologies including Powder Bed Fusion (PBF) and Directed Energy Deposition (DED). These methods among others have broadened the applicability of metal AM to critical industrial applications.
Highlighting the shift from traditional to metal additive manufacturing methods underscores technological progress and a change in mindset. Manufacturers now prioritize flexibility, digital integration, and the ability to quickly adapt to market changes
Understanding the Core Technologies of Metal Additive Manufacturing
Several critical technologies with unique applications and benefits power the processes necessary for metal additive manufacturing. Understanding these technologies is crucial for appreciating the versatility and potential of metal AM in industrial applications.
Powder Bed Fusion (PBF): Definition and Significance in Metal AM
PBF is a metal additive manufacturing technology that involves spreading a thin layer of metal powder over a build platform. A heat source, typically a laser (direct metal laser sintering, or DMLS) or electron beam, melts the powder according design. PBF is renowned for its precision and ability to create parts with complex geometries and excellent mechanical properties.
While PBF has garnered acclaim for its intricacy and quality, it is not without its drawbacks. Two primary limitations of this technology are its envelope size and build speed.
One limitation is that the envelope size is typically limited to under a 12-inch cube. This constrains the maximum dimensions of the parts that can be produced, making PBF less suitable for larger-scale applications. Additionally, the build speed of PBF processes is relatively slow, which can be a significant bottleneck for high-volume production needs.
Directed Energy Deposition (DED)
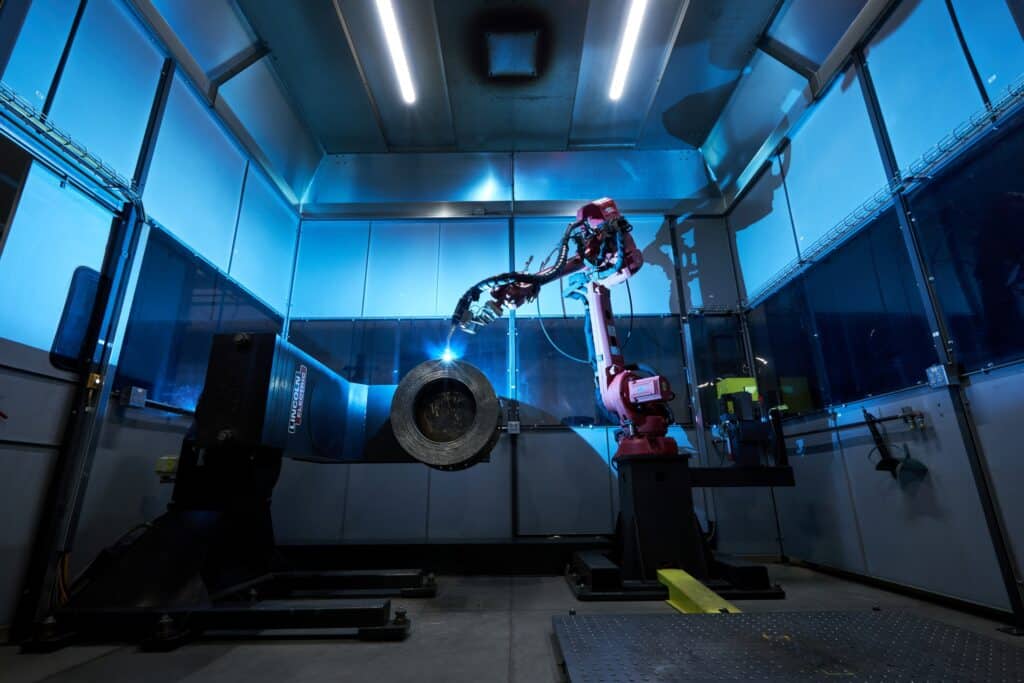
The limitations experienced in PBF have spurred innovations in metal additive manufacturing technologies. A notable example is Lincoln Electric’s commercialization of its large-scale 3D metal printing technology, Directed Energy Deposition (DED).
DED utilizes metal powder or wire fed into a focused energy beam. This energy beam then melts the material directly onto a build surface. Consequently, DED is particularly useful for repairing or adding material to existing parts. It is also highly effective for building large structures with complex geometries given the fine tuned additive process DED utilizes.
Binder Jetting and Other Emerging Technologies
Binder jetting is a process in which a liquid binding agent is used to join powder materials layer by layer. This technology offers a unique set of advantages for additive manufacturing. Parts be produced at high speed and relatively low cost, making it an attractive option for prototypes and production parts.
While binder jetting has traditionally been used with polymers and ceramics, advancements are now extending its application to metals. This promises to diversify the capabilities of metal AM further.
Solid-State Metal AM
Solid-state metal AM enables the fabrication of large-scale, high-quality metal parts at speeds far exceeding traditional methods, without the limitations of powder bed size or the need for vacuum systems.
This process significantly reduces residual stresses and avoids defects like porosity and hot-cracking, inherent in melt-based technologies.
Additionally, solid-state metal AM can handle a wide array of metals, making it a versatile option for a variety of manufacturing applications.
Lost-Wax Printing & Casting
Parallel to additive manufacturing techniques, lost-wax printing and casting offers a unique method for producing metal parts. By 3D printing a wax model and using it as a mold for casting metals, this technique merges traditional casting with modern 3D printing capabilities.
Although not a direct form of metal 3D printing, it is valued for its ability to produce detailed parts in nearly any metal, combining the precision of 3D printing with the material versatility of casting.
This method stands as an innovative bridge between old and new manufacturing processes, expanding the toolkit available to designers and engineers.
Materials in Metal Additive Manufacturing
The choice of material is a critical factor in the success of any additive manufacturing project. As the metal AM field evolves, so does the range of available metals, expanding the technology’s application across industries.
Stainless Steel, Titanium, Inconel, and Other Specific Materials Used in Metal AM
The use of specific metal materials such as stainless steel, titanium, and Inconel is pivotal in metal additive manufacturing (AM) processes due to their unique properties. Stainless steel, particularly 17-4 PH and 316LSi, is prized for its durability and resistance to corrosion, making it suitable for medical devices, automotive parts, and more.
Titanium alloys, including EOS Titanium Ti64 and Ti64ELI, offer an exceptional strength-to-weight ratio and biocompatibility, making them indispensable in aerospace and medical implants.
Inconel variants such as Nickel Alloy 617, 625, and 718 are renowned for their performance in extreme environments, providing resistance to oxidation and thermal expansion in applications like jet engines and turbine blades.
Beyond these, several specific materials have been identified as suitable for large-scale 3D metal printing technologies, such as Wire Arc Additive Manufacturing (WAAM). These include Aluminum-Nickel-Bronze, known for its excellent corrosion resistance and high strength-to-weight ratio, and Invar® 36, valued for its extremely low coefficient of thermal expansion.
Other notable materials tailored for 3D metal additive manufacturing encompass Nickel Alloy H282, known for its high-temperature structural applications, and various forms of stainless steel and titanium, each chosen for their distinct properties that meet the rigorous demands of specialized applications.
Exploration of Material Properties and Selection Criteria
The material selection criteria for an metal AM project involves a thorough understanding of the part’s intended use, including the mechanical stresses it will endure, the environmental conditions it will face, and any industry-specific demands it must meet.
Consider the fundamental properties of tensile strength, ductility, thermal conductivity, and resistance to corrosion or wear. The choice of material significantly impacts not just the performance of the finished part but also the manufacturing process itself, influencing factors such as printing speed, the need for support structures, and post-processing requirements.
Metal Additive Manufacturing in Action: Industry Applications
The versatility and efficiency of metal additive manufacturing have led to its rapid adoption across various sectors. Each industry benefits from metal 3D printing technology’s ability to produce complex, customized components quickly and cost-effectively, showcasing the technology’s transformative potential.
For insights into effective outsourcing strategies that complement your metal AM ambitions, explore our “Outsource Smarter” e-book.
Aerospace: Innovating for Efficiency and Performance with Tooling Applications
The aerospace industry’s exploration into additive manufacturing (AM) for tooling applications has led to groundbreaking advancements, particularly through the strategic use of Wire Arc Additive Manufacturing (WAAM). This innovative approach is revolutionizing the production of steel layup tooling used in the manufacture of composite laminations for unmanned aerial systems (UAS), showcasing significant efficiency and performance enhancements.
Achieving Cost and Time Efficiency: The GA-ASI Case Study
The collaboration between Baker Industries, a Lincoln Electric Company, and Lincoln Electric Additive Solutions (LEAS) with General Atomics Aeronautical Systems, Inc. (GA-ASI), highlights a pivotal development project.
This project explored the feasibility of WAAM for producing complex, accurate, vacuum-tight tooling capable of withstanding the stress and fatigue caused by repetitive autoclave cycles. The engineering teams’ collaborative review pinpointed WAAM as a potentially ideal solution for GA-ASI’s specific tooling challenges, demonstrating the adaptability and precision of metal AM in aerospace tooling applications.
Producing the World’s First 3D-Printed Invar® Cure Tool: A GE Aerospace and Lincoln Electric Collaboration
In a pioneering collaboration, GE Aerospace and Lincoln Electric embarked on an ambitious project that utilized WAAM to create the world’s first 3D-printed Invar® cure tool, a critical component in the aerospace industry known for its minimal thermal expansion properties.
By producing this tool, GE Aerospace and Lincoln Electric showcased the feasibility and efficiency of using WAAM for high-precision aerospace tooling, setting a new industry benchmark for manufacturing complex components.
Automotive: Accelerating Development and Customization
The automotive sector benefits from metal AM in several vital areas, including the rapid prototyping of new designs, producing complex, lightweight components that enhance vehicle performance, and customizing parts for luxury or high-performance models.
For automotive manufacturers, metal AM technologies facilitate agility in design and production processes, enabling faster iteration and customization without expensive tooling changes. Metal AM accelerates the development cycle, allowing a more responsive approach to market demands.
Medical and Beyond: Custom Solutions Across Sectors
Perhaps nowhere is the impact of metal AM more personally felt than in the medical sector. Additive manufacturing offers the ability to create custom implants and prosthetics tailored to the individual patient, improving outcomes and enhancing the quality of life.
Use of Metal AM for Personalized Medical Devices
From titanium dental implants to patient-specific orthopedic devices, metal AM’s precision and flexibility enable healthcare providers to offer solutions uniquely suited to each patient’s anatomy and needs, opening new possibilities in personalized medicine.
Large-Scale Metal Additive Manufacturing: Expanding Horizons
As metal additive manufacturing continues to evolve, one of the most significant advancements is its application in large-scale projects. Large-scale additive metal manufacturing (LSAMM) pushes the boundaries of what’s possible, allowing manufacturers to produce substantial components previously unthinkable due to the size constraints of traditional metal AM machines.
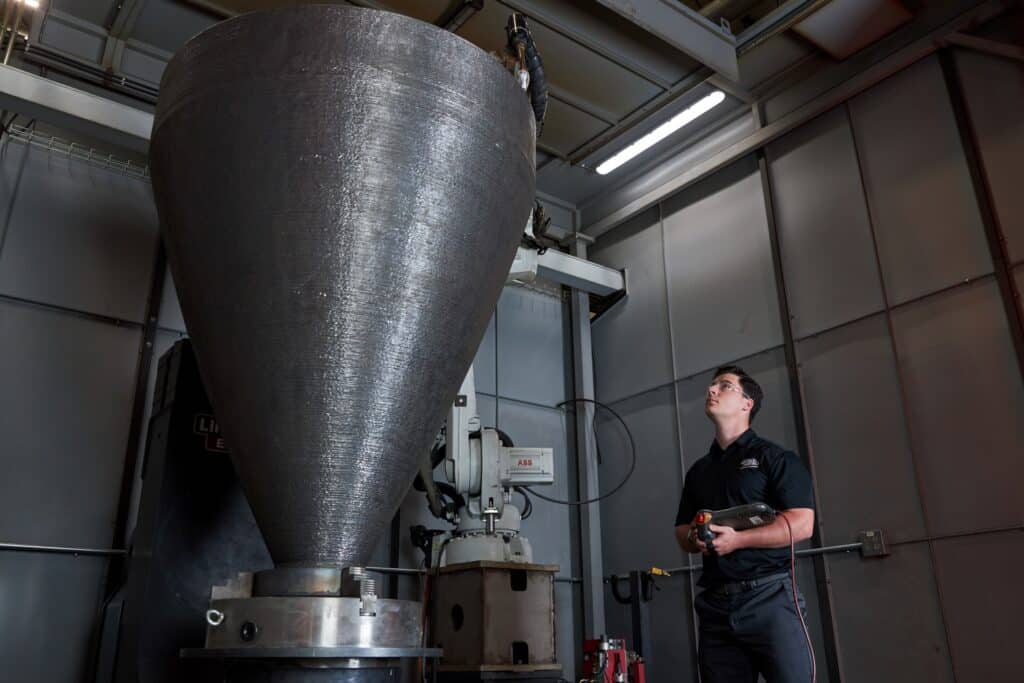
Overcoming Size Limitations with LSAMM
LSAMM technologies such as DED and large-format PBF systems have emerged to address the demand for bigger parts. These technologies are instrumental in manufacturing large-scale components with complex geometries, offering customization and efficiency that traditional manufacturing methods cannot match.
Applications and Advantages of LSAMM
The implications of large-scale metal additive manufacturing are profound, impacting a variety of sectors that require large, intricate components.
In the aerospace industry, LSAMM not only facilitates the production of substantial engine parts and structural elements but also plays a crucial role in manufacturing tooling for composite part fabrication. This application is particularly significant, as these tools are often very large and feature complex geometries that are more efficiently produced through 3D metal printing than traditional methods.
Challenges and Solutions in LSAMM
The scale of LSAMM introduces notable challenges, including the need for larger build volumes, higher power requirements, and advanced material handling systems. Ensuring uniform quality and mechanical properties across more significant parts demands precise control over the manufacturing process and innovative solutions to manage thermal stresses and distortion.
Collaborative Efforts to Advance LSAMM
The journey towards advancing LSAMM technologies is complex and multifaceted, requiring a concerted effort that spans machine design, process control, and material science.
A prime example of such collaborative innovation is the partnership between Lincoln Electric and Oak Ridge National Laboratories (ORNL), which epitomizes the synergy between industry leaders and research institutions in pushing the frontiers of additive manufacturing.
This collaboration is focused on commercializing Wire Arc Additive Manufacturing (WAAM) technology. Announced at the Department of Energy’s Advanced Manufacturing InnovationXLab Summit, the partnership aims to extend additive manufacturing capabilities to new materials, integrate data analytics for improved process control, and enable the rapid production of metal components at rates exceeding 100 pounds per hour.
The Business Case for Metal Additive Manufacturing
Adopting metal additive manufacturing offers technological innovation and compelling economic benefits. For businesses contemplating the integration of metal AM into their production processes, understanding the ROI and comparing it against traditional manufacturing methods is crucial.
Analyzing the ROI of Adopting Metal AM
The ROI from metal AM involves more than just the initial investment in technology and equipment. It encompasses improvements in production efficiency, reductions in material waste, and the ability to produce complex designs without costly tooling.
Additionally, metal AM’s capacity for rapid prototyping accelerates product development cycles, enabling quicker market entry and the potential for increased revenue.
Quantitative and Qualitative Advantages
The cost-effectiveness of metal AM comes into play through the reduction of material waste and the potential to reduce or eliminate tooling requirements, particularly for castings. This aspect, combined with lower inventory needs due to on-demand production capabilities and decreased labor costs from more efficient production processes, outlines the real economic advantages of adopting metal AM.
Qualitatively, metal AM offers substantial benefits that go beyond simple cost savings. It enables greater product customization and design flexibility, allowing for the creation of parts and components that were previously unfeasible with traditional manufacturing methods.
Additionally, it enhances supply chain resilience, providing businesses with a significant competitive edge in the marketplace. By leveraging these qualitative advantages, companies can not only meet but exceed market demands, driving innovation and customer satisfaction.
Comparative Analysis with Traditional Manufacturing Methods
Comparing metal AM with traditional subtractive manufacturing or casting processes reveals differences in cost structures and efficiency. While metal AM may have higher initial material and equipment costs, its ability to reduce waste, minimize assembly requirements, and shorten the design-to-production timeline often results in lower production costs for complex components and low-volume production.
Adopting metal AM allows companies to respond more agilely to market changes and customer demands. The technology’s customization capacity and suitability for efficiently producing small batches make it a powerful tool for companies looking to innovate and differentiate their product offerings.
Overcoming Challenges in Metal Additive Manufacturing
While metal additive manufacturing presents many opportunities for innovation and efficiency, it also has hurdles. Successfully addressing these complications is crucial for businesses to leverage the benefits of metal AM.
Post-Processing Requirements
One challenge is the need for post-processing, including heat treatment, support removal, and surface finishing. These steps can add time and cost to manufacturing but are essential for achieving the desired part quality and mechanical properties.
Quality Assurance and Consistency
Ensuring consistency and quality in 3D-printed metal parts necessitates precise control over the manufacturing process. Variabilities in material properties, machine parameters, and process conditions can affect the final product’s integrity, necessitating robust quality assurance protocols.
Solutions and Future Prospects for Metal AM Project Success
The path to successful metal additive manufacturing (AM) includes advanced monitoring and control technologies, developing standardized materials and processes, and investing in workforce training. These strategies are essential for overcoming the current hurdles within the industry and paving the way for its future growth.
Additionally, developing relationships with outsourcing partners experienced in metal AM such as Baker Industries can provide the expertise and resources needed to navigate the complexities of metal AM, from initial design to final production.
A testament to a successful metal AM project partnership can be seen in the collaboration between General Motors and Baker Industries. As highlighted by a prominent figure at General Motors, “Through collaboration with Baker Industries, we were able to develop GM’s 3D printing standards for lightweight measurement devices. Many of the measurement engineers, including myself, recommend that our vendors use Baker Industries for 3D printing because of their proven quality and repeatability, which our team has yet to find anywhere else.”
— Chairman, P.E.D. 114, General Motors.
Embracing Metal AM for a Competitive Edge
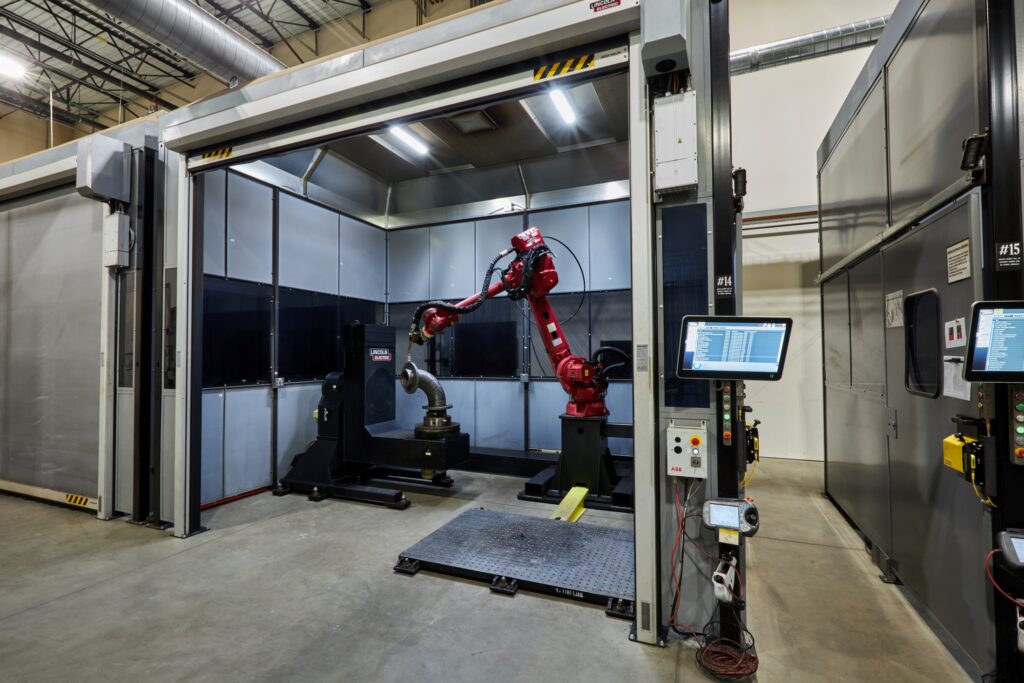
As companies continue to explore the potential of metal AM for producing complex, high-value components, the importance of strategic partnerships and knowledge sharing becomes ever more apparent.
To navigate the evolving landscape of additive manufacturing and address the associated challenges, partnering with an expert in the field is essential.
With our comprehensive expertise in additive manufacturing, CNC machining, fabrication, and engineering services, Baker Industries is ideally positioned to support businesses leveraging metal AM for a calculated advantage. Whether you’re exploring metal AM for the first time or looking to optimize your existing processes, our team is ready to assist.
For insights into effective outsourcing strategies that complement your metal AM ambitions, explore our “Outsource Smarter” e-book. It provides actionable plans and best practices for manufacturing teams looking to enhance operational efficiency and product quality through tactical partnerships.
To learn more about how Baker Industries can support your precision manufacturing needs or to discuss your project requirements, reach out to us at one of the links below.
- Talk to an expert: https://www.bakerindustriesinc.com/contact-us/
- Request a quote: https://www.bakerindustriesinc.com/contact-us/request-a-quote/