About Us
Over three decades of manufacturing excellence
Who We Are
An Industry-Leading Manufacturer
Founded in 1992, Baker Industries, a Lincoln Electric Company, is an industry-leading, award-winning supplier of advanced manufacturing and engineering services to OEM and Tier-1 leaders in the world’s most demanding industries.
Our legacy was built upon a steadfast commitment to quality, on-time delivery, customer experience, and innovation.
A Story of Incredible Success
Our History

1992
Brothers Kevin and Scott Baker open the doors to Baker Duplicating in Mt. Clemens, MI, with three employees and three small, used machines
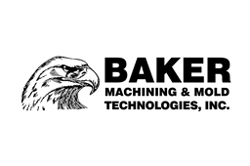
1998 - 2000
Invested in first five-axis CNC machine and rebranded to Baker Machining & Mold Technologies
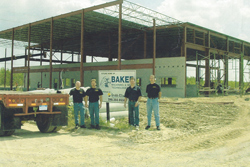
2005
Built a new 30,000 ft² facility in Macomb, MI, and expanded it an additional 30,000 ft² just three years later
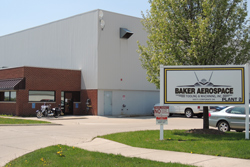
2010
Opened Plant 2, a 45,000 ft² facility originally dedicated to fabrication and aerospace build operations
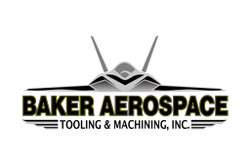
2011
Rebranded to Baker Aerospace Tooling & Machining to reflect growth in the aerospace and defense industry
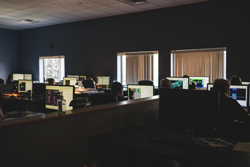
2012
Formed Baker Design Group, our in-house design and engineering team and invested in thermoplastic 3D printing technology
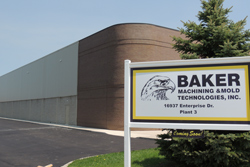
2013 - 2014
Opened Plants 3 and 4, invested over $20M into new equipment and facility improvements, and became a direct supplier to aerospace and automotive OEMs
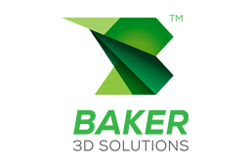
2015
Invested in metal 3D printing technology and launched Baker 3D Solutions to reflect growth in additive manufacturing
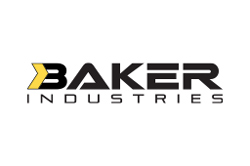
2016
Rebranded to Baker Industries to encompass all segments of the business under one name
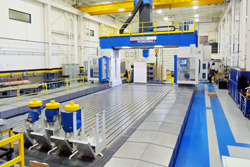
2017
Celebrated 25 year anniversary and invested in the company's two largest machines, the Emco MECOF Powermill and Ecomill

2018
Purchased Plant 5 and won Modern Machine Shop's Top Shop Award for Machining Technology
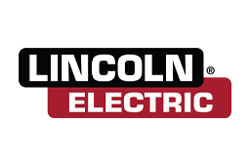
2019
Acquired by The Lincoln Electric Company to support its automation portfolio and metal 3D printing businesses
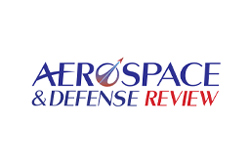
2022
Named Company of the Year for CNC machining by Aerospace & Defense Review magazine
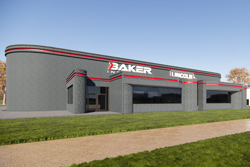
April 2022
Opened Plant 5, a 31,000 ft² facility for robotics and R&D
A Reputation for Manufacturing Excellence
Awards & Recognition
- Impact 100 Award | Emergent Defense Magazine
- Best Workplaces in Defense | Emergent Defense Magazine
- Top Honors, Environmental Award | Blue Origin
- Top Supplier, New Glenn Program | Blue Origin
- Company of the Year, CNC Machining | Aerospace & Defense Review
- Top Shop, Machining Technology | Modern Machine Shop
- (6) Performance Excellence Award | Boeing
- Outstanding Small Business Award | Lockheed Martin
- Top-Rated Supplier | GE Aerospace
- Top-Rated Supplier | Troy Design & Manufacturing (Ford)
- Preferred Supplier | SpaceX
- Diversification Award | Macomb County, MI
Our Experts
Meet the Baker Industries Team
FILTER BY DEPARTMENT
All
Bill Ednie
Senior Operations Manager
Brandon Rietz
Assembly & Inspection Manager
Burt Cronk
Program Manager
Chris “Slim” Keerl
Fabrication Engineering Manager
Deanna Meisel
Purchasing Supervisor
Doug Osborn
Estimator
Jeff Frent
System Administrator
Jeremy Glomski
Estimator
Jerry Lemke
Automotive Design & Engineering Manager
Jim Trieloff
Aerospace/Defense Design & Engineering Manager
Karrie Speagle
Office Manager
Mike Prohaska
Business Development
Rhondi Burke
Purchasing
Rich Rietz