Superalloys and their unique material properties are currently reshaping the future of manufacturing and engineering design for many industries.
As the global demand for superalloys continues to grow, manufacturers seek expertise in machining these heat-resistant, high-performance materials.
This article covers what superalloys are, why demand for these materials is increasing globally, and industries harnessing their distinctive attributes. We also address the complex challenges of working with such advanced materials.
What Are Superalloys?
Superalloys, often termed high-performance alloys, are a distinguished class of metallic materials engineered for exceptional resistance to heat, wear, corrosion, and oxidation.
Often nickel- or cobalt-based, these alloys are crafted to withstand extreme conditions. From enduring high temperatures to offering remarkable corrosion resistance, superalloys have properties that are tailor-made for demanding applications.
Their unique composition and low thermal conductivity set them apart in advanced materials.
Global Demand for Superalloys Is Increasing Now More Than Ever
Industries across the globe are striving to develop technologies and machinery that can operate under more extreme conditions while also being more reliable, efficient, and environmentally friendly.
Superalloys, with their remarkable properties, sit at the forefront of this evolution due to the following factors:
Versatility in Applications
From aerospace and automotive to medical and energy sectors, superalloys fit seamlessly across a wide range of industries. Their adaptability and resilience make them a preferred choice for diverse applications.
Global Infrastructure Growth
As emerging economies grow and invest in infrastructure, there’s a greater demand for materials that can ensure longevity and withstand challenging conditions. Superalloys fit this requirement, making them essential in the construction, transportation, and energy sectors.
Supply Chain Resilience
Recent global events have underscored the importance of resilient supply chains. Industries opt for materials like superalloys that offer reliability and reduce the need for frequent replacements or maintenance.
Economic Implications
While superalloys might come with a higher upfront cost, their long-term benefits in reduced maintenance, increased uptime, and extended equipment life cycle make them an economically viable choice for manufacturers.
Environmental Factors
With growing emphasis on energy efficiency and reducing carbon footprints, superalloys’ ability to operate effectively at high temperatures makes them ideal. This attribute translates to processes that require less cooling and, consequently, reduced energy consumption.
Key Industries Leveraging Superalloys
The exceptional properties of superalloys have rendered them indispensable across various industries. Let’s delve into a few sectors experiencing the highest demand for these advanced materials.
Aerospace
With its jet engines and advanced machinery, the aerospace industry heavily relies on nickel-based superalloys like Inconel 718. Essential for ensuring surface quality and maintaining structural integrity under immense thermal stress, superalloys are at the heart of aerospace innovation.
Their heat-resistant properties ensure aircraft components resist deformation, even in the intense heat of the cutting zone.
Power Generation
In environments as demanding as nuclear reactors or state-of-the-art gas turbines, the power-generation materials must consistently withstand high temperatures and intense pressures.
Superalloys rise to the challenge, guaranteeing peak performance and extended durability for power-generation components. Furthermore, they champion enhanced energy efficiency and steady power production.
Medical Technology
Superalloys, particularly nickel-based alloys, have been pivotal in medical technology. Their corrosion resistance and biocompatibility make them invaluable for applications ranging from surgical instruments to orthopedic implants.
Whether machining nickel components for a precision medical tool or crafting a titanium alloy implant, the surface finish and durability ensured by superalloys are unmatched.
Defense
The defense industry is synonymous with precision and reliability that leans heavily on superalloys. Their heat-resistant properties and high strength are vital for aircraft engines and naval vessels.
Ensuring the wear resistance and longevity of advanced weapon systems, superalloys, especially those with high nickel content, play a critical role in defense equipment.
Oil and Gas
The oil and gas industry faces challenges that only superalloys can tackle deep beneath the Earth’s surface, where high temperatures and high-pressure conditions reign.
For downhole drilling tools, these alloys’ low thermal conductivity and corrosion resistance enhance the durability and performance of critical components, ensuring optimization in oil exploration and production.
Machining Superalloys: A Deep Dive for Engineering Teams
While invaluable for their remarkable properties, superalloys present unique challenges in machining. Let’s delve into the intricacies manufacturers face when working with these advanced materials. For more information on working with superalloys on an upcoming project, visit:
https://www.bakerindustriesinc.com/capabilities/cnc-machining-services/
Work Hardening
Superalloys are known to work-harden rapidly. When a cutting tool interacts with the alloy, the material can harden at the point of contact, leading to increased tool wear and potential failure.
High Cutting Forces
The inherent strength and toughness of superalloys demand higher cutting forces, which stresses the cutting tools. It also requires robust and stable machine tools to handle the increased force.
Thermal Challenges
Superalloys retain heat rather than dissipate it. As a result, most of the heat generated during the machining process concentrates in the cutting zone, leading to elevated temperatures that can harm both the tool and the workpiece.
Abrasive Nature
Elements like chromium, tungsten, and cobalt give superalloys an abrasive nature, which can expedite tool wear, especially at the cutting edge.
Adhesion and Built-Up Edge
Superalloys tend to be adhesive to cutting tools, leading to a built-up edge. This edge can compromise the machined part’s surface finish and dimensional accuracy.
Requirement for Advanced Tooling
Conventional tool materials might not be up to the task of machining superalloys. Often, manufacturers need to invest in advanced tooling solutions, like cubic boron nitride (CBN) or polycrystalline diamond (PCD), to machine these alloys effectively.
Overcoming the Complex Challenges Superalloys Present to Manufacturing Production Teams
The art of machining superalloys is complex. While excellent for end-use, their remarkable properties present unique challenges during machining. The cutting force required, combined with the material’s work-hardening characteristics, can lead to rapid tool wear. However, with challenges come opportunities for innovation.
Modern carbide tools, carbide inserts, and advanced coolants are revolutionizing how the industry approaches superalloy machining. For more information on these tools and processes, be sure to visit the CNC machining services page for Baker Industries, a Lincoln Electric Company:
https://www.bakerindustriesinc.com/capabilities/cnc-machining-services/
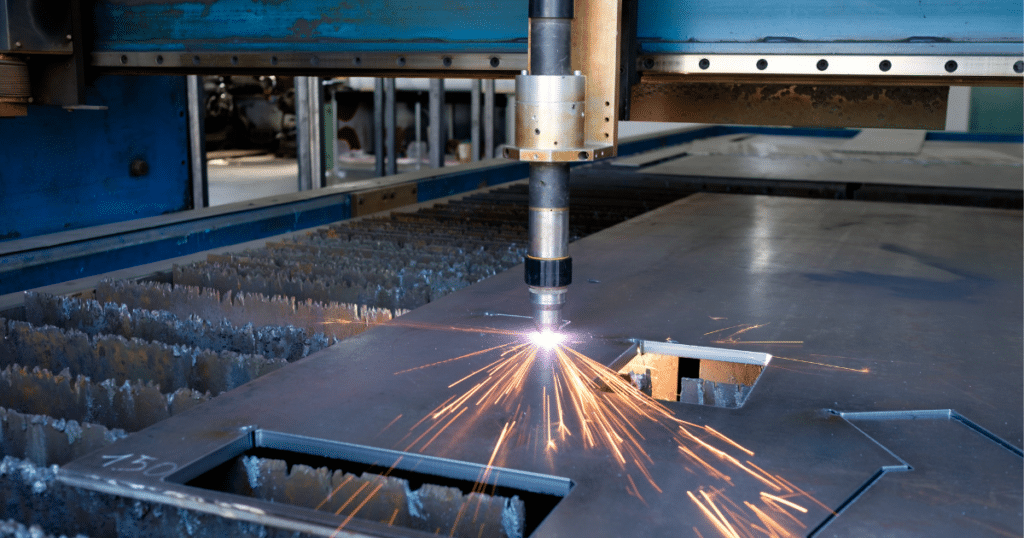
Find Industry-Leading Superalloy Machining Capabilities at Baker Industries
At Baker Industries, our machining services go beyond simply shaping materials. Using advanced machine tools and understanding the nuances of machining superalloys, we ensure that every workpiece mirrors perfection. From selecting the appropriate cutting tool materials to adjusting the cutting speed and depth of cut, we take every step with precision.
Delve deeper into manufacturing with superalloys and other difficult-to-cut materials with our comprehensive guide on the Best Practices for CNC Machining Hard-to-Cut Materials.
Conclusion
Machining superalloys is an intricate art form. As industries push the boundaries for materials that can withstand high temperatures and aggressive chemical environments and maintain their high strength, having a partner like Baker Industries becomes essential.
Our commitment to excellence, unmatched expertise, and ability to understand and adapt to challenges ensure that we’re not just a service provider but a partner in your success.
Contact us today with questions about an upcoming project or request a quote.
Talk to an expert: https://www.bakerindustriesinc.com/contact-us/
Request a quote: https://www.bakerindustriesinc.com/contact-us/request-a-quote/