The quest for a competitive edge through precision, durability, and efficiency is relentless for modern manufacturers. Laser welding is at the forefront of meeting these imperatives, a technique rapidly becoming the cornerstone of industrial fabrication.
The following sections delve into what laser welding is, why demand is growing, and how it’s advancing the frontiers of engineering to meet and exceed modern demands.
What Is Laser Welding?
Laser welding uses a focused, high-intensity light beam to melt and fuse metal or thermoplastics.
As a method, it stands out for its precision, allowing for intricate welds essential for complex designs and high-quality manufacturing standards. Here are a few of the key benefits:
- Precision: The capability to focus the laser to a fine point enables detailed joint configurations and precise weld seams.
- Speed: The welding speed outpaces traditional methods, contributing to greater production efficiency.
- Versatility: This technique can be deployed to work with a variety of materials and metals such as stainless steel and aluminum alloy.
- Minimal Heat Input: The process’s localized heat source reduces the thermal impact on the workpiece, maintaining its mechanical properties.
Why is the Demand for Laser Welding Capabilities Growing?
As the landscape of manufacturing shifts toward more sophisticated and refined processes, laser welding is at the forefront of this transformation. Industries increasingly prefer this technique because of its ability to meet the stringent requirements of modern-day production. Several reasons account for the growing adoption of laser welding in industrial applications:
- Advanced Material Compatibility: Modern manufacturing often uses advanced materials that traditional welding could potentially compromise. The precision and controlled heat application of laser welding joins sensitive materials without impairing their integrity.
- Complex Design Fulfillment: As products evolve to become more complex, so does the need for welding solutions that accommodate these intricate designs. The accuracy of laser welding is ideal for executing these sophisticated configurations.
- Unyielding Quality and Durability: Industries that cannot afford failures, such as aerospace and medical devices, require welds of the highest caliber. Laser welding ensures joints are robust and reliable, contributing to the overall safety and functionality of critical components.
- Enhanced Efficiency: The expedited process of laser welding means increased throughput. This can significantly shorten production times and reduce costs associated with labor and operations.
- Environmental Sustainability: Laser welding is a cleaner process overall. This reduces waste and lowers energy consumption, aligning with the growing imperative for sustainable manufacturing practices.
Recent Advancements in Laser Welding Technology
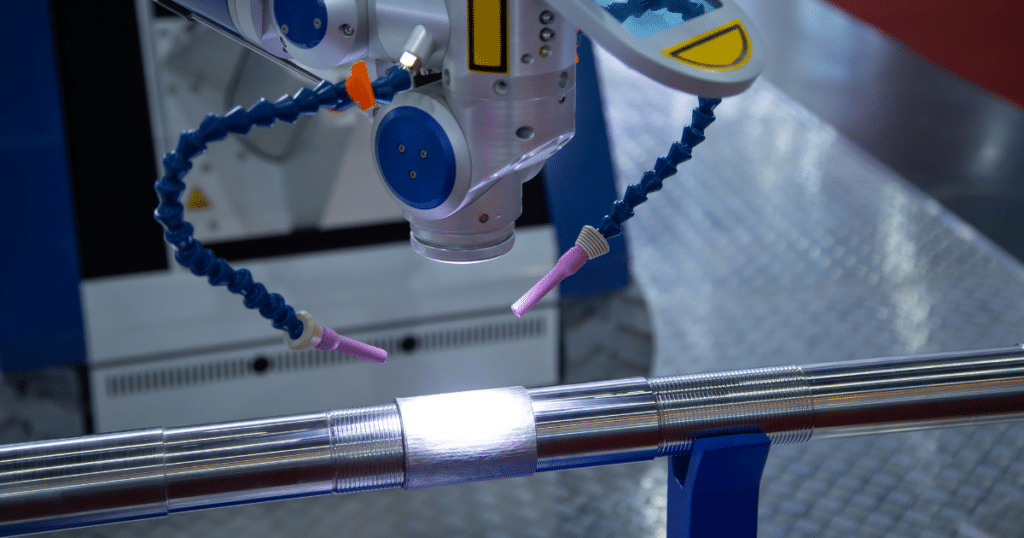
This field has benefited from remarkable technological advancements that have expanded its capabilities and applications:
- Fiber Laser Innovations: Introducing fiber lasers has elevated beam quality and energy efficiency. This is resulting in more precise and energy-conscious welding operations.
- Automation Enhancements: Integrating robotics and computer control systems has improved the consistency and efficiency of laser welding. This makes it even more of a reliable process for high-volume production.
- Adaptive Beam Shaping Technology: Recent developments include adaptive beam shaping, where the laser beam’s geometry can be dynamically altered during welding. This adaptability allows for customized welds that match the requirements of each project, resulting in improved weld strength and quality.
- Increased Process Monitoring and Control: Enhanced sensors and monitoring systems now offer real-time data and feedback during welding. This enables immediate adjustments and quality control, ensuring each weld meets stringent specifications with reduced error rates and waste.
The Laser Welding Process
The laser welding process unfolds through a finely tuned sequence, commencing with deploying a single, highly focused laser beam.
At the heart of this process, the laser beam provides an unparalleled heat source with pinpoint accuracy and intensity. Here’s a step-by-step breakdown of the laser welding process:
- Beam Focusing: The laser welding journey begins with the careful focusing of the laser beam to achieve the necessary power density. This focused beam acts as a minute flame, melting the base materials of the workpieces at the intended spot without the need for filler materials.
- Heat Control: Precision is vital in managing the heat input to reduce the heat-affected zones (HAZ), preserving the mechanical properties of the metals involved. Controlling heat is crucial to maintaining material integrity, particularly in sectors like aerospace and automotive, where precise specifications are critical.
- Automated Precision: The process benefits from automation, which ensures consistency and repeatability. Every laser motion is controlled and replicated with exactitude, guaranteeing uniformity across multiple welds.
- Deformation Prevention: With the strategic application of high-power density, the laser welding technique minimizes distortion, enabling the workpiece to retain its intended form post-welding. Preventing deformation is particularly advantageous for sensitive components or materials prone to warping.
- Rapid Cooling and Solidification: As the laser moves along the predetermined weld path, the molten materials cool and solidify, forming a strong bond. This quick cooling process is essential to achieving a weld seam that is robust, clean, and aesthetically superior.
- Final Inspection and Testing: Once the welding is complete, the workpiece undergoes a thorough inspection to ensure weld quality. Techniques like X-ray or ultrasound testing may be used to verify the integrity of the weld, ensuring it meets the high standards expected in precision engineering.
Applications Across Industries: The Transformative Impact of Laser Welding for Precision Manufacturing
The transformative power of laser welding extends across many industries, each benefiting from the precision and efficiency this technology brings to full-scale production and design.
This versatile welding process results in tailored solutions that enhance the structural integrity and performance of complex assemblies.
Repairing and Finishing 3D-Printed Components & Tooling
Some 3D printing technologies occasionally produce parts with uneven surfaces or voids. Because of its efficiency and minimal impact on the surrounding material, laser welding is commonly used to repair and fill these voids, maintaining the integrity of the part or tool and ensuring that its critical features, such as vacuum integrity, are achieved.
Aerospace Engineering
The aerospace industry operates on the frontier where exact precision is synonymous with safety and performance. The high-strength, low-heat input capabilities of laser welding make it a critical technique for aircraft and spacecraft assemblies and subassemblies.
Precision laser welding is particularly advantageous for working with common aerospace materials such as aluminum alloys and stainless steel, maintaining their mechanical properties and ensuring the longevity and durability of each component.
The Defense Industry
Equipment in the defense industry must perform reliably under the most rigorous conditions. Laser welding achieves deep penetration welds that provide the high-strength joins essential for military hardware.
This welding method can join diverse materials, including advanced, armor-grade metals, to meet the stringent durability and reliability standards required for defense applications.
Power Generation
In the energy sector, efficiency and uptime are closely linked to profitability. Laser welding’s rapid execution accelerates the construction and maintenance of power-generation equipment, increasing productivity.
This technology is instrumental in the manufacturing and repairing of components for wind turbines, power plants, and other energy infrastructure, offering precision and minimizing operational downtime.
Maritime and Shipbuilding
Shipbuilding benefits from the consistency and speed of laser welding, especially in handling thick steel plates crucial for vessel construction. The quality of laser welds ensures the structural strength required for ships to endure the harsh marine environment.
Laser welding contributes significantly to the longevity and seaworthiness of marine vessels by optimizing weld quality to minimize issues like porosity and corrosion.
Space Exploration
Space exploration demands flawless materials and components due to the unforgiving nature of space. The high precision and controlled welding that laser technology provides are invaluable in producing welds with minimal residual stress. This is a critical factor for space-bound equipment and vehicle designs.
From satellite assemblies to launch vehicles, creating complex, high-quality components is essential, with each weld playing a vital role in the success of space missions.
Through these diverse applications, laser welding is not just a manufacturing process but an enabler of innovation and advancement. This innovative technique is pushing the boundaries of what’s possible in engineering and manufacturing. It’s a testament to the ongoing evolution of technology, providing a competitive edge in an ever-changing industrial landscape.
Choosing a Laser Welding Partner for Your Precision Manufacturing Projects
Selecting a laser welding partner is as critical as the process itself. Choosing a company that understands the intricacies of the laser welding process and has the technology and expertise to apply it effectively is essential.
Baker Industries offers state-of-the-art laser welding services and a team of experts adept in the laser welding technique, ensuring the highest weld quality for your projects. Check out our fabrication and welding services page for more information on our specific laser welding capabilities:
https://www.bakerindustriesinc.com/capabilities/fabrication-welding-services/
Advancing Engineering Capabilities with Baker Industries
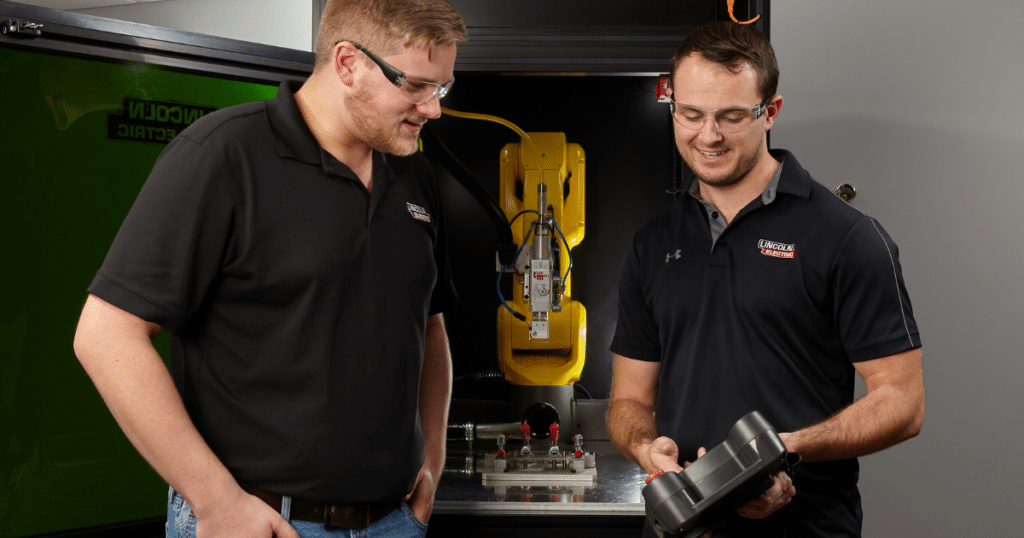
Laser welding is more than just a welding process; it’s a strategic advantage in the competitive arena of precision engineering. With Baker Industries’ laser welding expertise, you are equipped to meet and exceed the stringent demands of your industry.
Our comprehensive approach encompasses everything from design optimization to the final weld. Equipped with the latest laser welding technology, we can address the specific needs of your project, whether it involves working with aluminum alloy, stainless steel, or newly developed superalloys.
We invite you to advance your engineering capabilities with laser welding solutions by partnering with Baker Industries. We’ll work to ensure that every joint in your project is a benchmark of engineering excellence.
Contact us today with questions about an upcoming project or to request a quote.
Talk to an expert: https://www.bakerindustriesinc.com/contact-us/
Request a quote: https://www.bakerindustriesinc.com/contact-us/request-a-quote/